DICKINSON CABIN
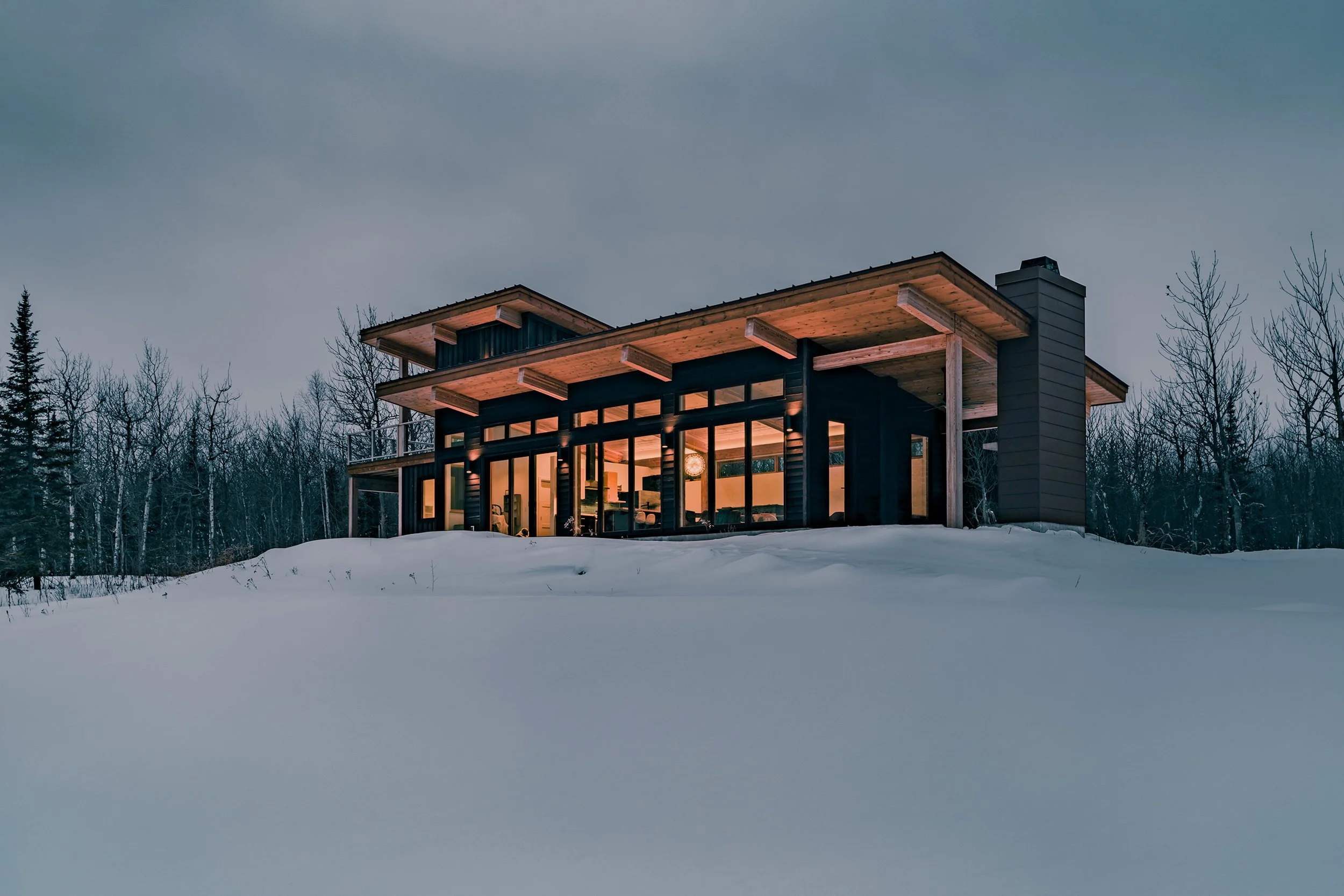
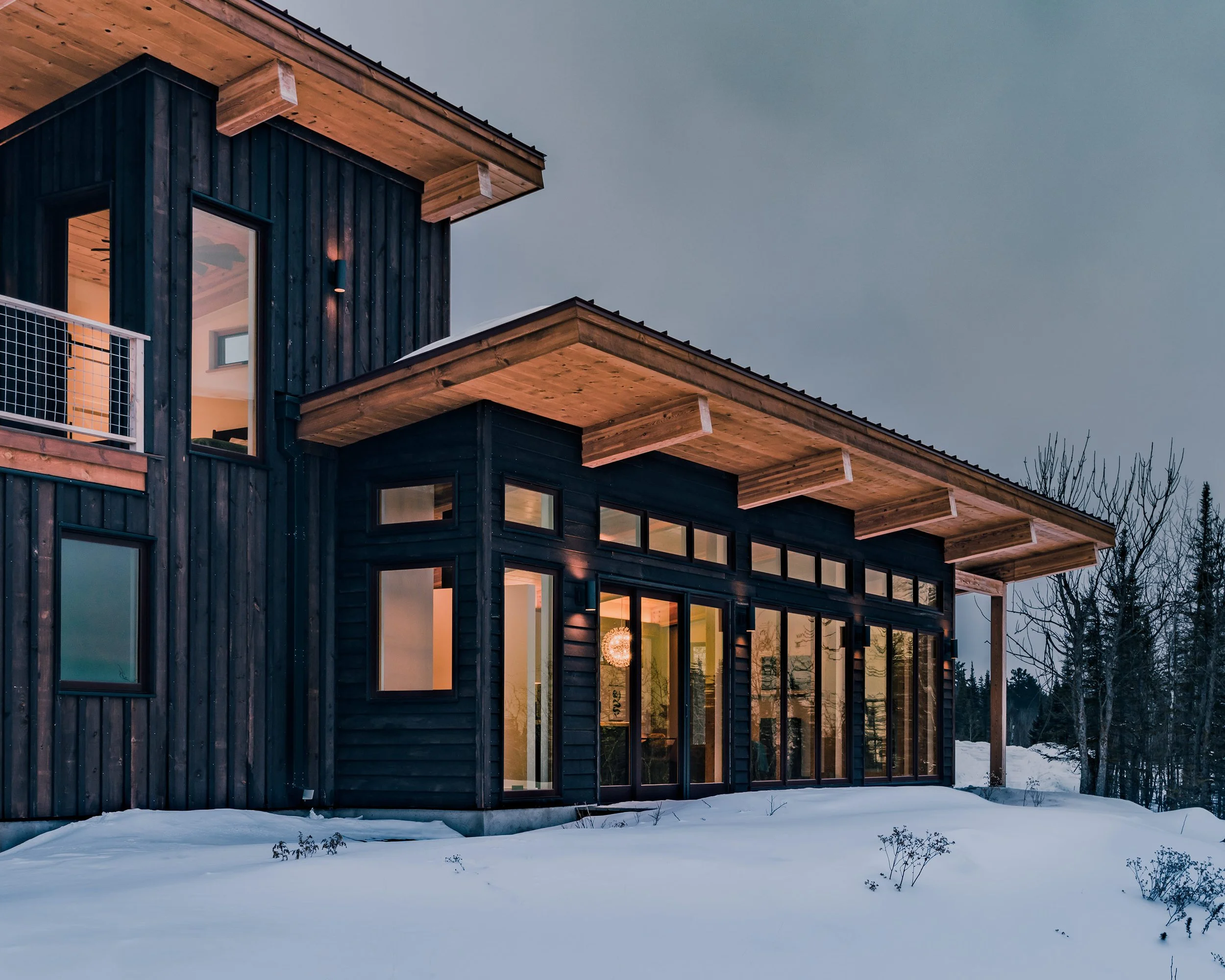
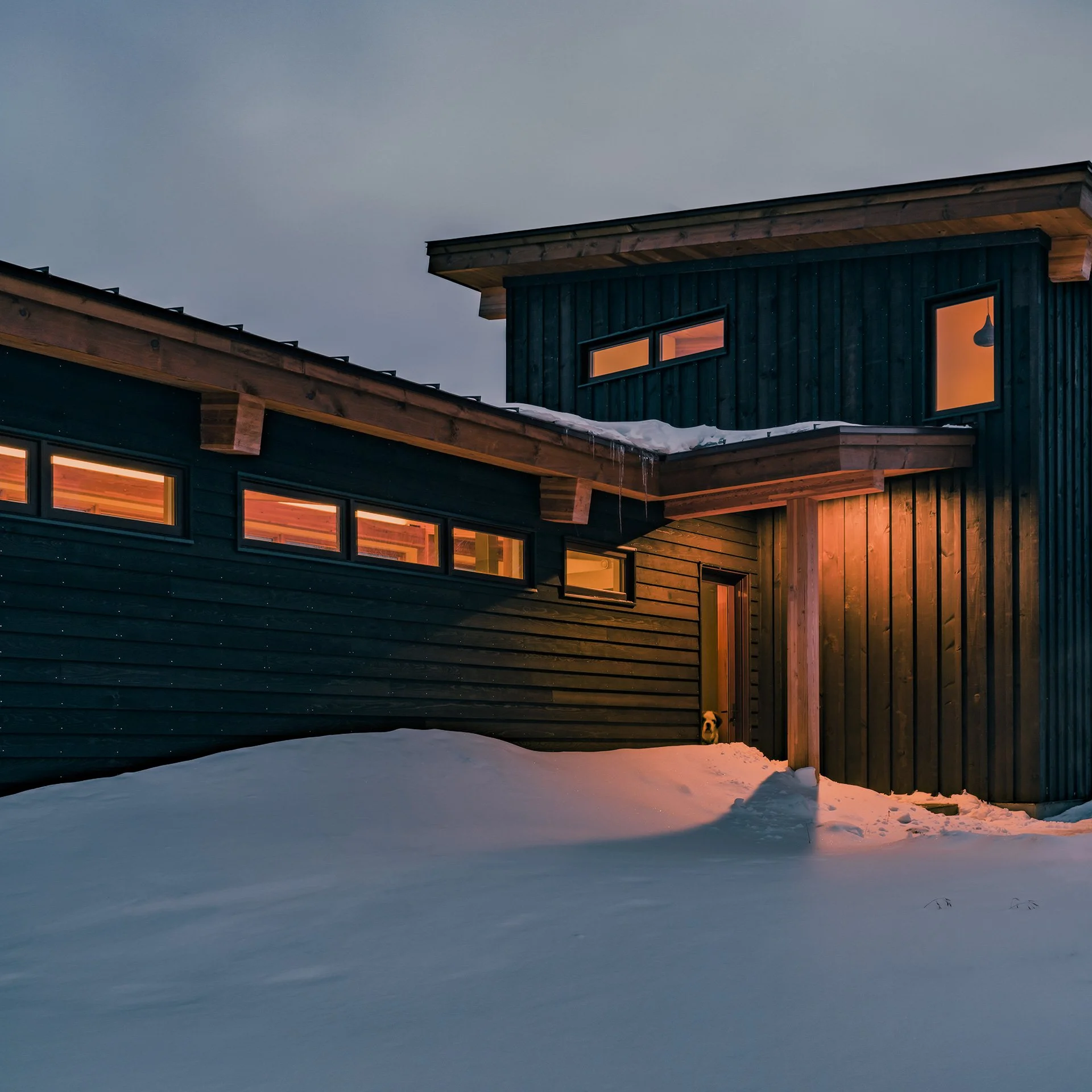

The Dickinson Cabin is a modern timber frame family retreat perched on a bluff overlooking Lake Superior.
PROJECT BASICS
LOCATION: Two Harbors, MN
SIZE: 1,400sf
PROGRAM: 3 Bed, 2 Bath
FOUNDATION: 8” ICF Walls, anchored into bedrock
STRUCTURE: Slab-On-Grade, Glulam Post & Beam, 2x6 Exterior Wall Framing
INSULATION: ECI R9 ZIP R-Sheathing, Cavity Closed-Cell Spray Foam, SIP Ceiling
MECHANICALS: Heat-Only Strategy, Combi-Boiler for DHW and Radiant In-Floor Heat, ERV
COMPLETED: December, 2021
HERS: 43 *before solar
CERTIFICATIONS:
PROJECT TEAM
OWNER’S REP: Counter Entropy
SITE ANALYSIS: Counter Entropy
BUILDING SCIENCE: Counter Entropy
CONCEPT ARCHITECT: UNFOLD Architecture
PROJECT ARCHITECT: Timberlyne
TIMBER FRAMING: Timberlyne
PREFAB WALLS: Timberlyne
GC/BUILDER: John Williams, Natural Home LLC
ENERGY RATER: Center for Energy and Environment
FINAL PHOTOGRAPHY: Hybrid Studio
INVOLVEMENT
Acting as an Owner’s Rep, Counter Entropy worked directly with the client to shepherd the project through all design and construction phases, bring in outside partners as needed.
Starting with a vacant undeveloped lot, we first explored several possible building site locations for the cabin with a goal to optimize the view towards the lake while maintaining privacy. Possible future buildings and infrastructure needs were also discussed. Deliverables included a site analysis and master plan.
After selecting a build site, we explored a wide range of ideas for the cabin designs searching for the right balance between the clients needs, the budget, and what the site had to offer us. Once a general direction had been found, UNFOLD Architecture was brought in to refine the concept. During this phase, we also began to define our building science approach for the mechanical systems and foundation, wall, & roof assemblies required to achieve the stated sustainability goals.
Timberlyne took over as the project architect to develop the final construction documents and supply the timber framing. Counter Entropy also worked with Timberlyne to develop a prefabricated wall system for the project, selecting ZIP R-Sheathing to provide a layer of exterior continuous insulation. SIP panels were selected as the roof strategy. The SIP roof combined with the prefabricated R-Sheathing walls provided a 100% thermally-broken exterior building shell and substantially minimized the construction time on-site.
Once the foundation was installed, Timberlyne sent materials and a crew to the site. They erected the timber framing and set the prefabricated wall and roof panels in a matter of days. A local high performance builder helped complete the remainder of the construction.
Counter Entropy visited the site several times during construction to provide quality control and construction administration tasks as required. I also ensured the design and construction were in compliance with the certifications being sought throughout all stages.
The Center for Energy and Environment was brought in to assist with the 3rd party verifications required at the end of the project.